Overview
Our journey began way back in 1970s when we manufactured the first single action hydraulic scrap baling press. Today, our vast experience, consistent quality up gradations & continuous R&D has led to the development of Fully Automatic, Continuous Production Hydraulic Scrap Baling Presses. Our baling presses enjoy excellent reputation in scrap yards, ferrous processing plants and non-ferrous metal melting plants. They compact virtually all the metal scrap such as sheet metals and aluminium scrap into square bales. These new generation metal presses / metal compactors set high standards for efficient scrap processing. Our continuous scrap baling presses are powerful and efficient in operation. These metal balers produce high-density bales. The higher pressing force and greater output makes these metal balers one of the fastest and the strongest bundle presses / baling presses in India.
For every application there is a suitable scrap baling press. Each scrap baler is equipped with two / three separately operating compactors that press the scrap material into compact bales. The drive and control concepts of the scrap baling presses allow an efficient operation with particularly low energy consumption and maximum throughput capacity.The carefully planned construction of these metal balers is sturdy and durable due to extensive wear protection. The common wear parts of the compactors can be easily replaced, without having to remove the complete compactor units. The operation and troubleshooting can easily be performed on the multi-information PLC display of the metal baler. The terminal consists of a large display that shows all process-relevant information & status reports.
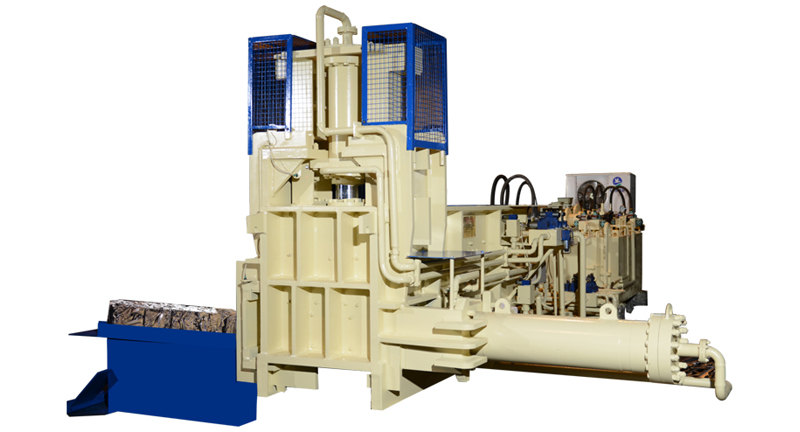
Salient Features:
1. Continuous production of bales resulting into high productivity
2. Each scrap baler is equipped with compactors that presses the scrap into high density bales
3. The drive and control concepts of the scrap baling presses allow an efficient operation with particularly low energy consumption and maximum throughput capacity
4. The carefully planned construction of these metal balers is sturdy and durable due to extensive wear protection
5. The common wear parts of the compactors can be easily replaced, without having to remove the complete compactor units
6. The operation and troubleshooting can easily be performed on the multi-information PLC display of the metal baler
7. The terminal consists of a display that shows all process-relevant information and status reports
8. Easily replaceable wear-resistance plates are provided for the long life of the feeding chamber
9. Shearing blades are provided on the edges of the chamber & the partition slide to shear over sized material
10. Efficient after sale service
Benefits:
1. Our“Continuous” balers are easy & economical in operation and run continuously once switched on. These continuous balers compress the scrap and transform them into dense bales one after the other against continuous charging of scrap inside the feeding hopper via grabber / inline conveyor. Our baling presses are best suited to meet the high-end production requirement and produce considerate cost savings during the scrap transportation. Such metal balers enable maximum feeding of scrap in the EAF during one heat. These balers are available in various sizes and with various capacities & can compact virtually all metal scrap such as sheet metals and wire scrap into dense square bales.
Operating Procedure
1. Once the scrap is charged on the top of partition slide, it opens and closes, thereby allowing the scrap to enter the lower chamber for baling and also shearing any oversized scrap
2. The scrap is first compressed from the rear end by the main compression cylinder/s
3. The scrap is then compressed from the top and the two dimensions of the bale gets fixed
4. The side cylinder then compacts the scrap from the third direction thereby forming a high-density bale
5. Once the desired pressure is reached, the bale ejection takes place and all the cylinders reverse to their home positions
6. Meanwhile the scrap for the next cycle is charged by the conveyor / grab or manually
7. The partition slide opens again and the scrap enters the baling chamber
Data Sheet:
1. Production depends upon quality & grade of scrap and scrap charging rate
2. Above data achieved under ideal working conditions
3. Jain Hydraulics reserves all right to change the specifications at any time without any prior intimation
4. All data is indicative and not binding
Three Way Continuous
Hopper Size (InchxInchxInch) | Bale Size (InchxInch) | Main Motor (HP) | Bale Weight (KG) | Production/Hr (Tons) | ||||||
M.S. | Aluminium | Copper | Paper | M.S. | Aluminium | Copper | Paper | |||
48×30 | 10×10/12×12 | 80 | <=50 | <=20 | <=50 | <=40 | <=4 | <=1.5 | <=4 | <=3 |
60×40 | 12×12 | 120 / 160 | <=150 | <=50 | <=150 | <=50 | <=9 / <=15 | <=2 / <=4 | <=9 / <=15 | <=4 |